Greying Fellow
A greying fellow reflects on...
Improving construction productivity
George Bothamley continues his series on the continuous unmet need to improve productivity
A PROJECT that required innovation by necessity was a new service water storage reservoir for a scheme that had a compliance date that had become imminent because approval for capital investment had been delayed. The then-current norms for design and construction would have resulted in considerable overrun of the compliance date, and a number of the innovations were initiated to overcome this. Other innovations were introduced – not of necessity, but a result of the team culture to seek to do better.
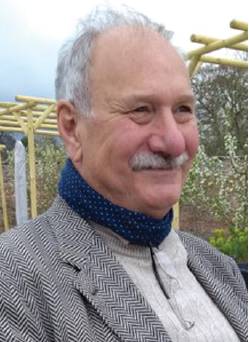
Option selection meetings established that providing the storage volume required with a deeper reservoir of a smaller footprint would be significantly cheaper. This is partly because the unit cost of walls is less than the unit cost of base and roof, and partly because the proportion of usable height is greater (the depth for headroom at the top and sludge collection at the bottom are the same regardless of total depth).
The hydraulic profile of the existing storage and distribution system appeared to dictate a very small depth, but one of our engineers came up with a novel design involving a reflux valve in the supply mains that enabled a deeper reservoir with a smaller footprint. This innovation resulted in a 20% reduction in cost, mostly in the reduced use of unsustainable and environmentally unfriendly materials like concrete.
The water company concerned owned large tracts of land for which it had a policy of divestment. It was therefore reluctant to buy new land beyond the bare minimum area for new assets.
As a result of this policy, we often bought a piece of land for the asset and then rented an adjacent piece of land for at least its purchase price to use as a laydown area during construction, and with extra costs in managing the hand-back to the owner. We were able to buck the trend in this instance on the basis that we needed to acquire the land before we could be sure that the reduced footprint was indeed feasible and for mitigation if it was not. We used the extra land for permanent storage of surplus excavated material, saving costly and environmentally unfriendly export to landfill, used it as a laydown area during construction and left an ecologically landscaped area which could be used as a future laydown area.
One of the water company’s engineers had come across submarine access doors on Swiss storage reservoirs built into mountainsides, and thought they might be a good solution to the increased security required for strategic assets by avoiding rooftop access hatches. We utilised them on this reservoir and found that they were slightly less expensive than roof hatches and saved considerable time, mostly because they could be installed whilst the roof was still under construction.
One curious lesson learned from them was a rare incidence of ‘right first time’ not being the cheapest and quickest way. I found this personally interesting, because my wife, rightly, accuses me of being selective at what I excel at. This is sometimes because the effort is too much for me and sometimes because I lack interest. But here is an instance of not excelling being productive.
Some of the construction methods we used saved time and money, whereas others saved time but at additional cost
The opening in the concrete walls was formed to a normal fine positional tolerance for concrete of 5mm, but it was later found that the submarine door frames required a positional tolerance of 2mm. The rectifying solution was to bolt a dummy frame to the concrete wall, apply an epoxy resin filler in the gap between wall and frame, then after curing replacing the dummy frame with the submarine doors. I knew from experience on a service reservoir some years earlier how difficult it is to achieve 2mm tolerance on concrete surfaces. The resident engineer interpreted a specification that mentioned 5mm and 2mm positional tolerance for concrete to require 2mm tolerance everywhere.
He also interpreted concrete surface to mean all faces, so that a ground slab had a bottom surface. We power floated blinding concrete to satisfy his interpretation. Our substantial time and money claims were only settled after many months when our chief engineer demonstrated how achieving fine tolerance of concrete surfaces required abnormally fine measurement and many iterations of fixing and refixing formwork. Getting it roughly right and then doing some rectification work was the quickest and cheapest way for the submarine doors.
Some of the construction methods we used saved time and money, whereas others saved time but at additional cost. An example of time and cost saving was starting excavation when the new structure footprint was established but before design was complete. This shortened the construction programme with a little extra risk that had a mitigation plan.
An example of time saving but at extra cost was using prefabricated reinforcement. It saved time because the company who welded the reinforcement mats could produce bending schedules and fabricate and deliver reinforcement in less time than our designers could produce bending schedules to get in the queue for cutting and bending at traditional suppliers. Time was saved, but the extra cost of the material was significantly more than that of the reduced fixing cost and overall time saving. We took the idea from one of our fellow framework partners who considered it a major cost saving initiative.
They produced a video of speeded up erection of factory-made reinforcing panels with a digital clock spinning round with the increasing hours saved and alleged cost saving. But I have never worked on a structure where reinforcement was on the critical path after the first structural concrete pour. I would have stopped the clock after a couple of days.
Factory assembly
Factory assembly has its place in improving construction productivity, but not to the extent that its evangelical adherents claim. Many years ago, I did some analysis of pre-casting concrete with a project manager who had encountered it extensively in the Middle East to overcome climate and skilled labour issues.
I have never worked on a structure where reinforcement was on the critical path after the first structural concrete pour. I would have stopped the clock after a couple of days.
We found that pre-casting was very often cheaper if the casting yard was on site but almost never cheaper from a remote factory. So, if there is space, pre-casting on site was often a good option, whether constructing complex one-off components on the ground instead of in the air or having a production run for repetitive components. Off-site fabrication for concrete reinforcement or steelwork components may be a good solution where space is at a premium, such as railways, inner-city locations or crowded existing plant installations. But not always. Following the financial crash it was common to construct storage tanks with precast concrete from Ireland. I priced scores of these for a water framework and only once was it a cheaper solution than in-situ concrete.
The work in joining the units together in a water-retaining structure consistently made them less productive, and I would guess that the shift in currency exchange rates has made them even less so. For technical and mechanical components factory fabrication can be efficient providing damage during site installation to items such as sensitive instrumentation can be avoided and quality checks at the factory and on delivery eliminate the need for post-installation rectification and re-work. In all cases of factory assembly rigorous approximate cost comparison including risk assessment should be done to assess that it is indeed cheaper.
From outline scheme approval to storing drinking water in service took significantly less time for this reservoir than was normally spent on construction alone. Some of the things described would be good for productivity anywhere. Others merely saved time and allowed a statutory date to be met. One of these was bringing the reservoir into use at an earlier than normal stage of construction completion, such as before backfilling around and over the reservoir. Whether because of staff relaxation and exhaustion after meeting an urgent deadline or delaying non-critical items out of their best sequence, the end out activity was not as productive as we would have wanted. But overall, the scheme demonstrated how challenging targets can be achieved and productivity improved.
Addressing productivity issues on overspending projects
Halfway through a five-year capital maintenance programme for renewal of water assets up to £4m individual scheme value, the end cost forecast indicated overspend causing slippage into pain share, an indication of declining productivity.
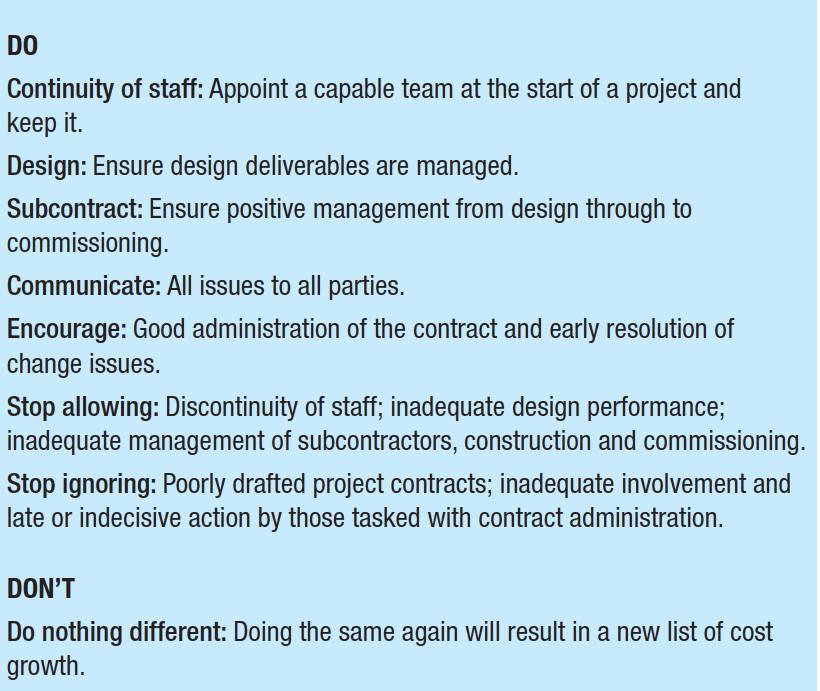
Table 1
To address this unsatisfactory situation the commercial surveying team first undertook some analysis of the cost forecasts. From a portfolio of about 150 schemes, they considered the 10 best and 30 worst for cost growth over the previous eight months. (This reflected the proportion of well and poorly performing schemes.)
From this a small team of commercial surveyor and delivery managers ascertained the incidence of features and behaviours on the poorly performing schemes and those on the well performing schemes.
They found eight features which were common on poorly performing schemes but largely absent from well performing schemes, and five features that were common to most of the well performing schemes and absent or rare in the poorly performing ones.
The team then devised an action plan of things to do more of, things to avoid as shown in Table 1. The list could have been all DO. The single DON’T is a double negative as a result of the consensus view being that there must be dos and don’ts.
This is contrary to a concept that being positive leads to improved productivity. I learned this from a tutor on a workshop for mentoring and developing staff. Her background had been in teaching young offenders and primary school children.
To illustrate that it is more productive to ask for what you want, not say what you don’t want she recounted how she regularly took a primary school class to the public library, walking across town in crocodile file.
She announced one week that they would not be going to the library because it was closed for redecoration, by which time the children were lined up in crocodile file at the door. They didn’t listen to the negative.
Reliability centred maintenance uses a multi-step decision making approach asking questions such as ‘is the residual asset life low’, and is ‘the failure rate and consequence of failure high’.
Soon after, on a trip to Melbourne I noticed the positivity of Australian street signs compared to the UK. In the Botanical Gardens, where the UK would have signs ‘Keep off the Grass’, ‘No Ball Games’, ‘No Cycling’ the Australian version was ‘Walk on the Paths’, ‘Carry the Ball’, ‘Wheel the Cycle’.
The ‘No Entry’ sign on the road outside was the same as in the UK except for the plate underneath. The UK’s says ‘No Entry’, Australia’s ‘Wrong Way! Go Back’. It’s not easy to be always positive, but I do like the notion that if you always ask people to do what you want, they will spend so much time doing things well that there isn’t the time left over to do things badly.
The intention of our report was not to establish a cost for each feature identified, but to highlight behaviours that should be encouraged or eliminated. The message was ‘get the behaviours right and the cost savings will follow’. The initial data for the analysis of features common to poorly performing or well performing projects was a list of forecast costs and gain/pain share sorted from best to worst performance.
By splitting this into well performing, moderately performing and poorly performing categories we could assess the impact of, say, improving five poor performers to moderate and five moderate performers to good. Or 10 of each. Or 15 of each.
The intention of our report was to highlight behaviours that should be encouraged or eliminated. Get the behaviours right and the cost savings will follow.
To reinforce the behaviours identified as leading to improved productivity it was considered that a further initiative was needed if the desired shift in productivity was to be achieved. So we borrowed from a sister framework a 10% cost saving initiative. We required each scheme to report on pro forma changes they could contemplate to reduce the scheme cost by 10% from the previous year’s end cost forecast, how they were developing the ideas, when they were implemented and the cost saving realised.
Most projects came up with a sufficiency of ideas. For instance, a major pumps replacement scheme had (1) make a permanent pipework connection for temporary bypass pumps instead of repeated temporary connections; (2) find a slicker installation method to reduce the extent and duration of scaffolding; (3) investigate timing of HV switchgear replacement to minimise temporary generation for power outages; (4) adjust programme to avoid costly accelerated delivery of pumps; (5) resequencing programme to reduce construction and commissioning duration.
As with many of the schemes, some of these were not viable, some produced less saving than forecast and some delivered expectations or more. Overall, the 10% saving proved elusive, but significant improvement in productivity was achieved.
Planning for continuous improvement
The team referred back to these initiatives in planning for continuous improvement for the next five-year capital maintenance programme. This was by a combination of seeking to adapt and develop what had previously been done to suit the new workload and looking for new methods and techniques that had emerged elsewhere.
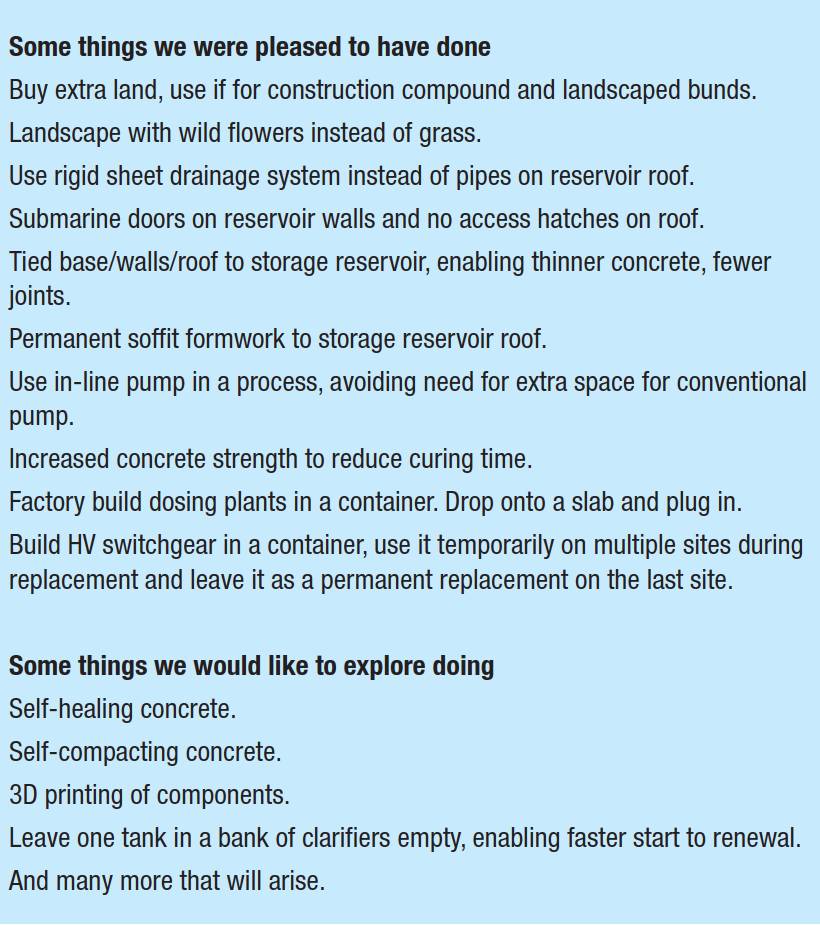
Table 2
Examples of adaptation were clustering, batching and streaming work to improve project delivery by taking into account geography, people, work type and work sequence; operating cost modelling to get the best whole life cost solution; standardisation (factory thinking); targeted improvement – looking for innovation in the areas of largest spend. New concepts included reliability centred maintenance (RCM) and better option selection.
RCM uses a multi-step decision-making approach asking questions such as; Is the residual asset life low? Is the failure rate and consequence of failure high?
At each step, if the answer is no, capital replacement is not justified and only those assets where all the answers are yes get capital expenditure approval.
With option selection, on the one hand the client perceived that our process was slow and expensive and on the other hand it was pointed out in reviewing our process that it was not clear that we always selected the best option.
We developed a step-by-step process whereby the overall solutions were assessed and for those that were practical, the potential solutions for each component assessed in terms of viability and cost including risk.
The best component solutions were selected resulting in selection of the best value overall scheme. Reasons for discarded solutions were recorded so that they should not be reintroduced on a whim.
Risk management was proposed using root cause analysis, which is essentially a similar process.
Table 2 shows some of the things we did and some more that we proposed.
By now some will be business as usual and others viable for adaptation in the search for continual improvement in productivity.
Continuous improvement, capital efficiency, increased productivity, cost saving, risk management and innovation are all concepts that require doing something different that benefits performance.
Incremental change can be immediate; radical change takes time. There is no need to continue doing the same until radical change arrives.
They all require innovation of one sort or another, ranging from ‘little I’ low level incremental change to ‘big I’ game changing radical change. Incremental change can be immediate; radical change takes time. There is no need to continue doing the same until radical change arrives.
A core part of achieving any increased productivity is metrics. Quantify everything in monetary terms; set a baseline of what it costs now; assess what we expect it to cost, so that we choose the option that gives best monetary value; monitor the actual costs, so that the savings are real; measure and celebrate our success and set a new baseline for the future.
We have now looked at how we looked forward to adapt our methods to apply them to new situations. Next, we will look at how looking backwards to identify ideas to develop these methods.
George Bothamley FCInstCES